Epoxy resins, or polyepoxides, are a class of reactive prepolymers and polymers that contain epoxide groups. The epoxide functional group is also collectively called epoxy. They are a family of basic components or cured end products of epoxy resins.
Epoxy resin is a basic component that possesses high mechanical, high thermal, high-class adhesive, and good chemical resistance properties. These make it highly useful for various applications, like coating, molding and casting, adhesives, sealants, and many more.
- History of Epoxy Resins
- Different types of Epoxy Resin
- How to use Epoxy Resin Effectively?
- Uses & Benefits of Epoxy Resins
- Safety Precautions While Dealing With Epoxy Resins
- Chemistry of Epoxies
- FAQs
- What is epoxy resin?
- What are the different types of epoxy resins?
- How do I know which type of epoxy resin to use?
- What are the benefits of using epoxy resins?
- What are the different properties of epoxy resins?
- What are the factors to consider when choosing an epoxy resin?
- Why is epoxy resin important?
- How do I use epoxy resin?
- What is an epoxy resin used for?
History of Epoxy Resins
The first commercial attempts to prepare epoxy resins from epichlorohydrin were made in 1927 in the United States (US). Credit for the first synthesis of bisphenol-A-based epoxy resins is shared by Dr. Pierre Castan of Switzerland in 1936.
Dr. Castan’s work was licensed by Ciba, Ltd. of Switzerland. One of the three major epoxy resin producers worldwide. Ciba epoxy business was spun off and later sell in the 1990s, which was subsequently sold in 2003 and became Advanced Materials Now the Advanced Materials business unit of Huntsman Corporation Company of the Texas United States (US).
Dr. Greenlee’s work for the firm of Devoe-Reynolds of the United States. Reynolds, which was active in the early days of the epoxy resin industry, was sold to Shell Chemical (now Momentive Specialty Chemicals Plants, formerly Hexion and others).
At least two epoxide groups are the low molecular weight pre-polymers or higher molecular weight polymers that are normally contained. The epoxide group is also sometimes referred to as a glycidyl or oxirane group.
A lengthy range of epoxy resins is produced in industries. The raw materials for epoxy resin production are today largely petroleum-derived; although some plant-derived sources are now becoming commercially available (For Example, plant-derived glycerol used to make epichlorohydrin).
An important criterion for epoxy resins is the epoxide content. This is commonly expressed as the epoxide number, which is the number of epoxide equivalents in 1 kg of resin (Kg). Which is the weight in grams of resin containing 1 mole equal to an epoxide (g/mol). One measure may be simply converted to another:
Equivalent weight (g/mol) = 1000 / epoxide number (Eq./kg)
With the other classes of thermoset polymer materials, blending different grades of epoxy resin, as well as the use of additives, plasticizers are common to achieve the desired processing. The use of blending, additives, and fillers is often referred to as formulating.
Different types of Epoxy Resin
There are three types of Epoxy Resin.
- UV Resin.
- Polyester Resin.
- Polyurethane Resin.
UV Resin
UltraViolet (UV) Resin is different from other resins, in overall it is made up of only one component. UV cure resin sets very quickly, usually within a few minutes, and doesn’t need to be combined with a hardener component. Other epoxy resin cures without any external aids, but UV resin requires exposure to ultraviolet light to cure.
Benefits of using UV Resins
- UV resin has a fast drying time than other types of epoxy resin.
- All the relevant parts are already combined, there is no need to mix them with hardeners.
- As the product only begins to set when UV light is applied to it, this allows you a longer working time with this product.
Disadvantages of using UV Resins
- UV resin sadly has a very restricted shelf life and expires within 6 months if not used/set. This is of course when it is in its unset state.
- You require a UV lamp light to set the product, which can be a costly piece of material.
- Compared to other types of resin, UV resin is almost expensive.
Applications of UV Resins
The applications of UV resin are a lot as you can choose to flow it over the item you wish to coat. And you can also tone or color the UV resin before use.
The most remarkable part is how the UV resin dries or sets. This particular type of resin will only be set correctly if disclosed to UV light. So you’ll have enough time to make whatever you wish and then expose it to UV light to set it.
The time required to set the item depends on the size of the piece and the thickness of the resin.
Polyester Resin
Polyester resins are unsaturated synthetic resins, used in building boats, swimming pools, and ponds. Polyester resin is one of the most popular thermoset resins and is known for its water resistance and overall strength.
Benefits of using Polyester Resin
- Polyester resin is best for the budget. It’s cheaper.
- You can control the drying time by the amount of hardening solution used when forming the resin.
- As previously mentioned, polyester resin is waterproof and thermoset resin.
Disadvantages of using Polyester Resin
- All types of polyester resin are known for their pungent smell.
- The overall mixing process can be more technical and therefore more difficult than other types of resin, as it is up to you to determine the desired setting time and levels when integrating the two elements.
Application of Polyester Resin
Like all other types of epoxy resins, you are required to combine the two elements to utilize the polyester resin. It is important to measure the two parts to ensure the correct consistency.
polyester resins are used for flat roofs, pipes, and storage tanks to make them waterproof. It is also used in components for the marine, construction, aerospace, and even in automotive industries.
Polyurethane Resin
Polyurethane resins are copolymers formed when alcohol called polyol reacts with an isocyanate – (dual or polymeric) in the presence of appropriate additives and catalysts. Polyol molecules contain three or more reactive hydroxyl groups.
As a wide variety of diisocyanates and polyols can be made to react for polyurethane resin production, polyurethane resin applications are numerous and diverse, spanning a wide range of industries.
Polyurethane resin can be used for casting molds as it is a very variable resin type. It can be used to create a variety of products. Thanks to its easily operated properties. It is a solid resin that becomes very hard when set by heat, which is utilized in a variety of industries. For example, one can find many polyurethane products within appliances, and it is also widely used within the automotive industry.
Benefits of using Polyurethane Resin
- This particular type of resin is very heat resistant, once it has been healed or set.
- When setting there is only a minimal amount of shrinking.
- Polyurethane resin can be easily mixed, as it has very good flow properties, which also makes it easy to use when filling an area.
Disadvantages of using Polyurethane Resin
- Polyurethane resin is highly sensitive to steam which can result in reactions such as foaming.
- Once you have set and cured the resin you are unable to melt it.
- During healing a very unpleasant scent is given off.
Application of Polyurethane Resin
Polyurethane resins are widely used as wood and floor surface coating, plastic coatings, and sealers because of their outstanding water resistance, chemical resistance, and toughness.
It can be used in creating mold casting to make different products/parts too.
How to use Epoxy Resin Effectively?
You need to take care of two things to use Epoxy Resin effectively.
- Prepared workspace
- Mix epoxy resin carefully
Prepare your workspace for your success
Before you start using any kind of epoxy resins, ensure your workshop is clean, dry, and free from any dust.
The temperature should be around 20-25°C.
If you’re outside in an open area, use a tent to create a temporary workshop and use a dry heat source to get the temperature up and down. But avoid using propane or diesel-based heating systems.
Pro tip: In hot temperatures, use a slow hardener to increase cure time.
Mix epoxy resin carefully
Make sure that you can mix your resin and make it strong and at the correct balance. It is necessary that both elements are balanced and well-mixed. Otherwise, the epoxy may not able to heal.
For the best result use a mixing stick which will also help you remove the dry resin. If any unconfident epoxy resin is visible in the pot once you’ve pushed out the excess, you’re not mixing in detail enough.
Uses & Benefits of Epoxy Resins
Epoxy resins are used in a variety of industries due to their refusal of thermic stress and water, which makes them particularly effective to stop product degradation over time.
They are known for their solid sticky qualities and they can be used with miscellaneous materials including mirrors, stone, metal, wood, fabric, cement, fiberglass insulation, and more.
They also serve as a key element in the fire impending layer used in merchant and industrial facilities.
Epoxy resins are ideal contributors to a variety of applications because of their strength, durability, lightweight properties, and long-standing safety track record.
They are versatile and can be used to make a variety of products, including adhesives, potting compounds, coatings, sealants, and paints.
Below are some of the things that epoxy resins are being used in to provide strength, durability, and long-lasting properties.
Epoxy resin uses in non-renewable/renewable energy
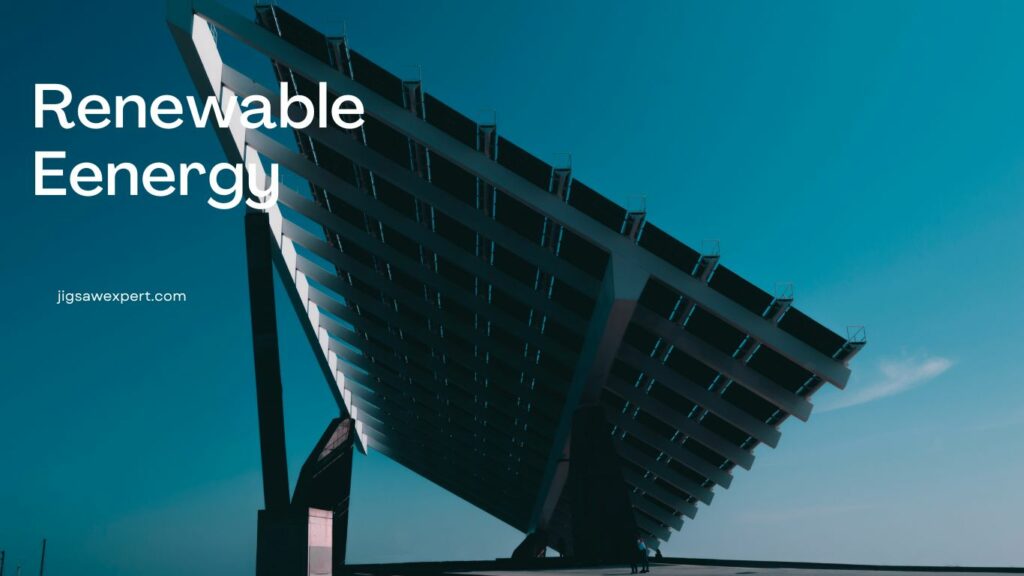
Epoxy resins are used in complex coatings in the production, transformation, and division of various types of renewable and non-renewable energy power.
The renewable wind energy power sector is one key area in which epoxy resins are highly valuable.
Relevant Materials created with epoxy resins are required components in offshore island wind energy farms due to their strength and low material, lightweight, and high mechanical grip-hold.
Epoxies are used to coat the steel bodies of the wind turbine poles, produce their blades, and protect the body structure of solar energy power stations from saltwater corrosion. Which can increase the electricity power by up to 30% compared to the same weight of steel core cable.
Epoxy resins also help in energy transportation by making the cables and components easier and softer.
Epoxy resin uses in building & construction
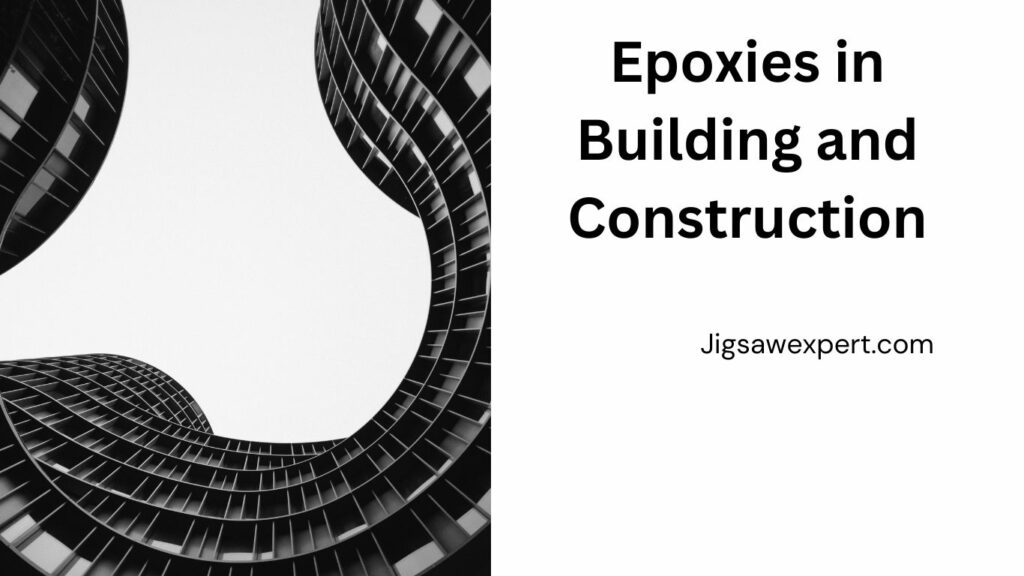
Within the construction industry, epoxies are used to strong and secure structure parts, engineering adhesives, floor coating, and paints.
Their appearance helps to improve strength, provide a longer lifetime, and lessen the need for repainting and development, ultimately providing economic benefits.
Epoxies are more heat and chemical-resistant than most glues and can stick to wood, metal, glass, stone, and some plastics.
The primary areas for the application of epoxy resins in construction main projects are coatings, flooring, concrete restoration, crack repair, and as joint material for tiles.
Epoxies are so operative in these environments because their soft nature allows coated floors to be sanitized by stronger cleaning products.
Epoxy resin uses in automotive & transportation
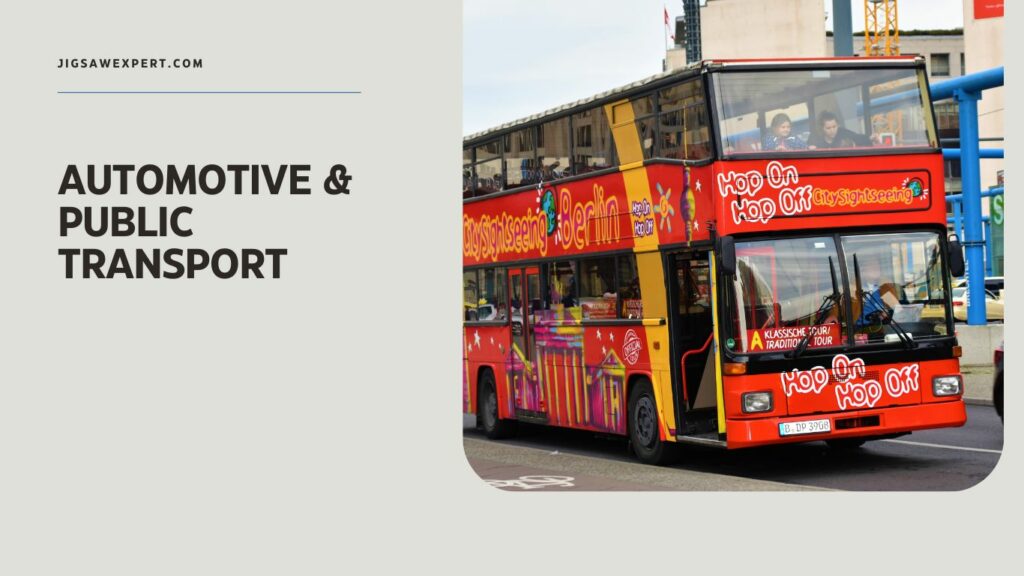
Epoxy resins are used in automotive industries to provide fixing to metal and add resistance to rust and corrosion on the body and other important metal parts of vehicles.
A thin, nonfatal, epoxy-based coating is applied as a primer. Which is then healed and covered with a topcoat that protects the primer from UV light.
The rail and oceanic sectors also benefit from the use of epoxy resins. They have the ability to replace steel in key machinic material. Thus lowering the overall weight.
They also reduce corrosion and other degrading elements, adding life to trains and boats.
Epoxy resin uses in aerospace
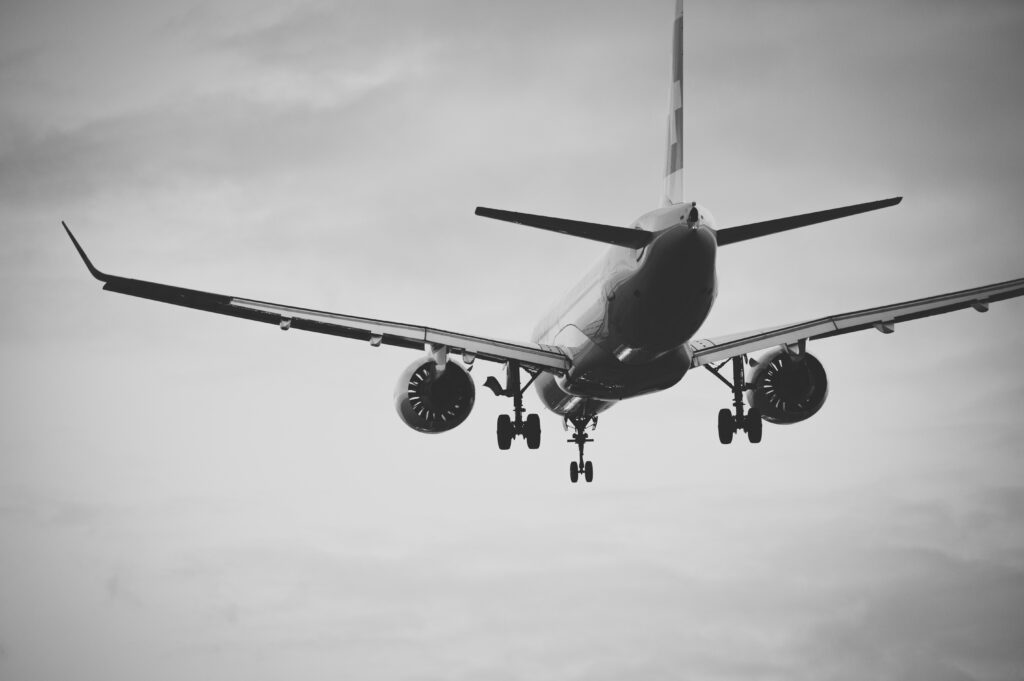
Epoxy resins are used in aircraft and satellite systems to bind materials like glass and carbon. This results in fiber materials that are strong and lightweight. Which improves strength, flexibility, and performance.
The epoxy resins can also be made to resist the extreme temperatures experienced by aircraft.
Safety Precautions While Dealing With Epoxy Resins
Epoxy resin is so creative way to make art-craft and jewelry. You can use it also to make resin pots, business card holders, beach crafts, and bunches of these things.
Although most epoxies are non-toxic you should take care of your safety first.
Wear Gloves
You need to take care of your hands to protect them from the hardener liquids of epoxy resin. After all, these are chemicals.
No products found.
It’s no different than protecting yourself from others chemicals in your home like bleach, paint, or weed killer.
So before starting work, you can use Nitrile Gloves Latex gloves, or any other chemical-resistant gloves. They work great to protect your hands from the resin kits, and if you are careful when removing them, you can reuse them another time as well.
Wear a Plastic Apron
Let’s face it when we are working with epoxy, spills, and drips happen. Not only is it terrible to ruin your favorite shorts, but oftentimes you don’t even know what you’ve done with them. Until those favorite shorts come out of the dryer.
No products found.
What kind of resin apron is the best?
I prefer to use a PVC Apron. Should resin get on the apron; you can wipe it off or peel it off once it cures.
Wear a Safety Goggles
I hope you’re not bathing in this kind of stuff. But it may spill in your eyes. You should protect your eyes by wearing safety goggles.
No products found.
Although the way some other companies talk about their products, they would make you believe you could use them without any permission. But safety glasses are important to keep your eyes protected from epoxy resin.
Wear a Respirator
First of all, many resins do not need a respirator when dealing with them.
You can find this information on any epoxy resin with a safety data sheet in the personal protection and in the precautions section.
But, once again, we are talking about chemicals. That means you can’t be too safe and it’s risky if you don’t use the respirator.
Tip: Just because you can’t smell anything doesn’t mean dangerous steam isn’t there.
No products found.
If you want to use a respirator, make sure it is a NIOSH-approved respirator for smoking.
I get my respirator and cartridges from the PK Safety store. They have several styles and designs. Their customer service is excellent in helping you get the one you need based on how you are going to use it.
Pro Tip for Ladies: You may do smoothly great with a small respirator mask. They will tell you that most of their clients need a medium size, but they must be working with a lot of big woodchoppers. Mine is a small size and fits to wear perfectly.
Chemistry of Epoxies
Epoxies are formed by the reaction of a hardener and an epoxy resin or by the reaction of resins with themselves. Epoxy resins are a broad class of prepolymers and polymers containing more than one epoxy group, also often referred to as glycidyl or oxirane.
Most epoxy resins are industrial products derived from petroleum and are themselves the result of a reactive process involving epoxy units (cyclic ethers with three atoms in a ring).
Depending on the type of reaction used to make them, cured epoxy resins can have different chain lengths and degrees of purity, corresponding to different molecular weights. They can be either low molecular weight liquids like honey or high molecular weight solids. Their molecular weight often determines their potential uses and applications.
Epoxy resins are relatively stable at room temperature and only acquire their final properties when they react with curing agents such as polyamines, aminoamides, and phenolic compounds.
The most common epoxy resins are based on the reaction of epichlorohydrin with Bisphenol A. This reaction converts the basic building blocks to another chemical called Bisphenol A diglycidyl ether, a low molecular weight resin more commonly known as BADGE or DGEBA. It represents the smallest type of epoxy resin.
Currently, BADGE-based resins are the most widely and commercially available resins of this type.
Common hardeners for epoxy resins
The following are the most commonly used hardeners for epoxy resins.
Amines: Most commonly used. They react at room temperature or slightly higher.
Anhydrides: Used at elevated temperatures. Very low viscosity and long “open time”. They can be used with mineral fillers, e.g. for high-voltage electrical insulators.
Phenols: React at elevated temperatures (130-180°C), and usually need a catalyst. Epoxides can react with their own phenolic groups. It is used for powder coating.
Thiols: They are very reactive even at lower temperatures. Perfect for home DIY adhesives and chemical anchors where heating is not an option. Thiols have a pungent odor.
FAQs
Last update on 2025-07-05 / Affiliate links / Images from Amazon Product Advertising API. Note: Jigsaw Expert may earn a commission when you buy through links on our site.